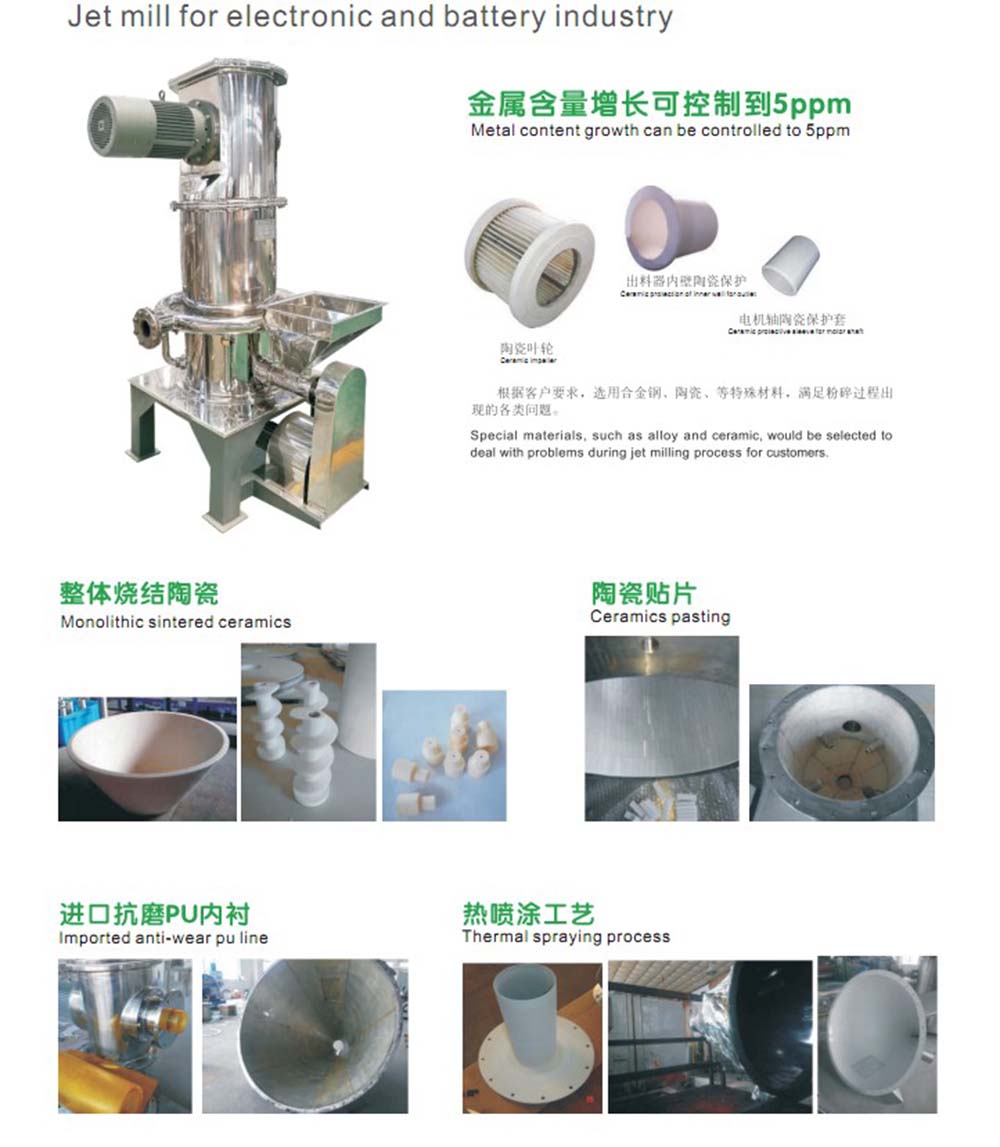
model | QDF-120 | QDF-200 | QDF-300 | QDF-400 | QDF-600 | QDF-800 |
Working pressure (Mpa) | 0.75~0.85 | 0.75~0.85 | 0.75~0.85 | 0.75~0.85 | 0.75~0.85 | 0.75~0.85 |
Air consumption (m3/min) | 2 | 3 | 6 | 10 | 20 | 40 |
Diameter of fed material ( mesh) | 100~325 | 100~325 | 100~325 | 100~325 | 100~325 | 100~325 |
Fineness of crushing(d97μm) | 0.5~80 | 0.5~80 | 0.5~80 | 0.5~80 | 0.5~80 | 0.5~80 |
Capacity (kg/h) | 0.5~15 | 10~120 | 50~260 | 80~450 | 200~600 | 400~1500 |
Installed power (kw) | 20 | 40 | 57 | 88 | 176 | 349 |
Product Description
Technical parameter
The flow chart is standard milling processing,and can be adjusted for customers.Flow chart of Fluidized-bed Jet Mill
Application Samples
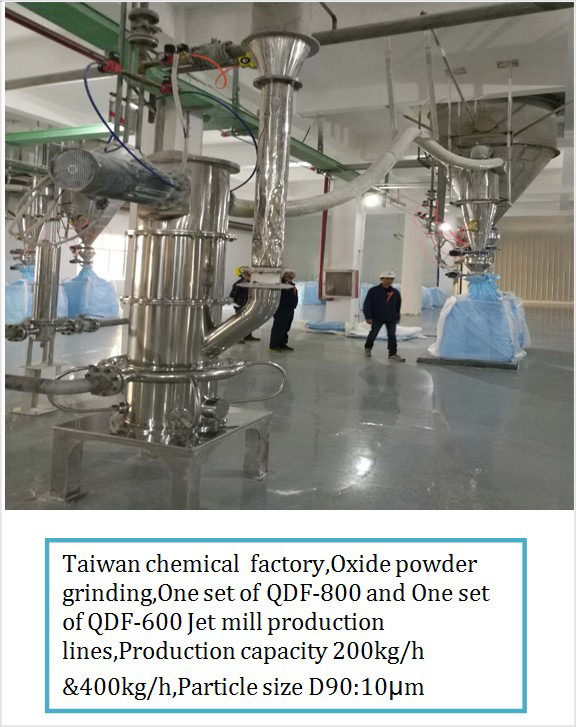
Material & Application
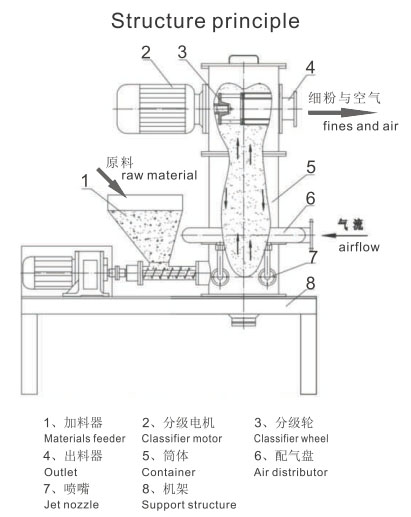
Operational Principle
The material enters the crushing room through the material feeder. The compression air nozzles into the crushing room in high speed through the specially equipped four crushing nozzles. The material gains acceleration in the ultrasonic jetting flow and repeatedly impact and collide at the central converging point of the crushing room until it is crushed. The crushed material enters the grading room with the upflow. Because the grading wheels spin at high speed, when the material ascends, the particles are under the centrifugal force created from the grading rotors as well as the centripetal force created from the viscosity of the airflow. When the particles is under the centrifugal force larger than the centripetal force, the coarse particles with larger diameter than the required grading particles will not enter the inner chamber of the grading wheel and will return to the crushing room to be crushed. The fine particles that comply with the diameter of the required grading particles will enter the grading wheel and flow into the cyclone separator of the inner chamber of the grading wheel with the airflow and get collected by the collector. The filtered air is released from the air intaker after the filter bag treatment. The pneumatic pulverizer is composed of the air compressor, oil remorer,gas tank, freeze dryer, air filter, fluidized bed pneumatic pulverizer, cyclone separator, collector, air intaker and others.Performance Features
Detail show Ceramics pasting and PU lining in whole grinding parts contacting with products to avoid scrap iron taking in lead to the invalid effect of terminal products.1.Precision ceramic coatings, 100% eliminate the iron pollution from material classification process to assure the purity of the products. Especially suitable for iron content requirements of the electronic materials, such as cobalt high acid, lithium manganese acid, lithium iron phosphate, Ternary Material, lithium carbonate and Acid lithium nickel and cobalt etc battery cathode material. 2. No rise in temperature: The temperature will not increase as the materials are pulverized under the working conditions of pneumatic expansion and the temperature in the milling cavity is kept normal. 3.Endurance: Applied to materials with Mohs Hardness below Grade 9. since the milling effect only involves the impact and collision among the grains rather than the collision with the wall . 4.Energy-effective: Saving 30%-40% compared with other air pneumatic pulverizers. 5.Inert gas can be used as media for milling flammable and explosive materials. 6. The whole system is crushed, the dust is low, the noise is low, the production process is clean and environmental protection. 7. The system adopts intelligent touch screen control, easy operation and accurate control. 8. Compact structure: the chamber of the main machine composes the closes circuit for crushing.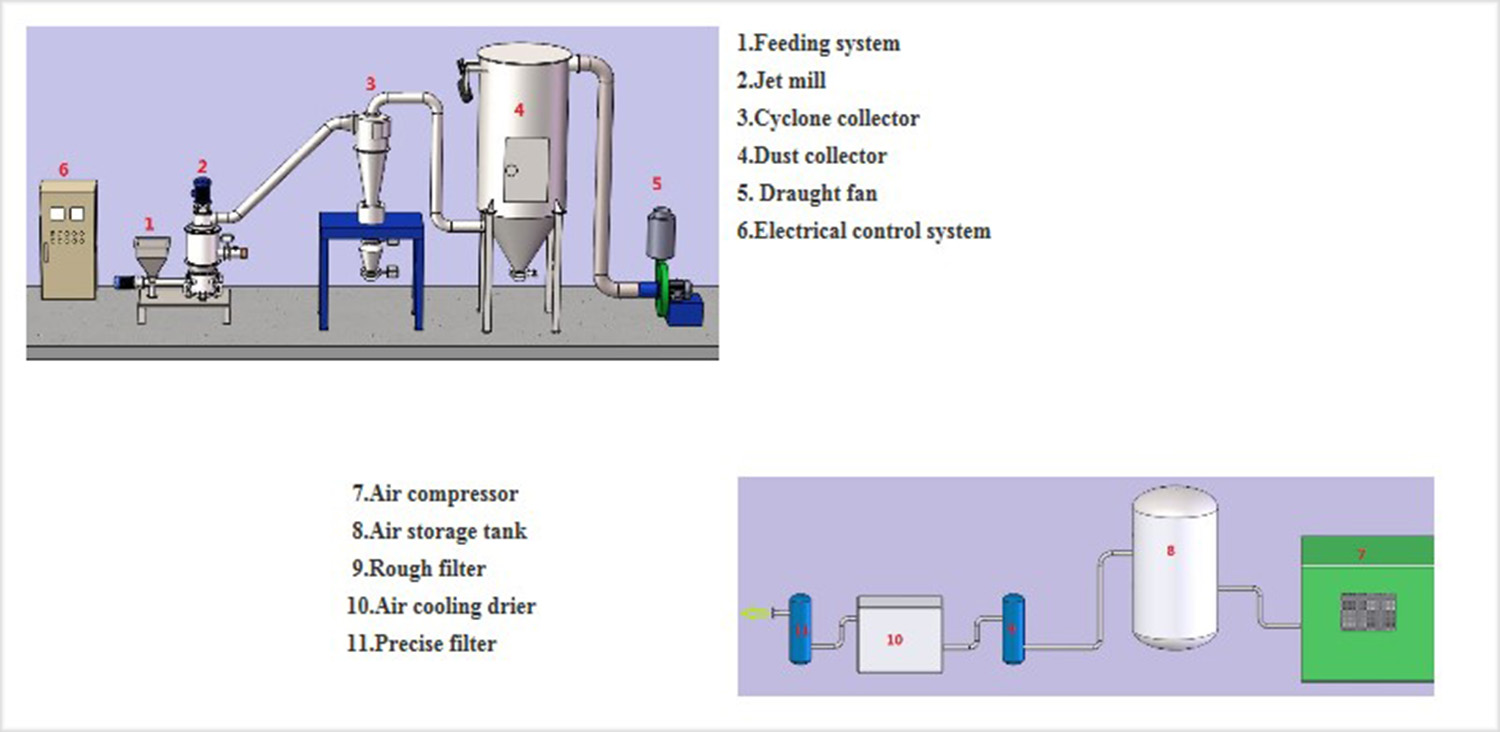
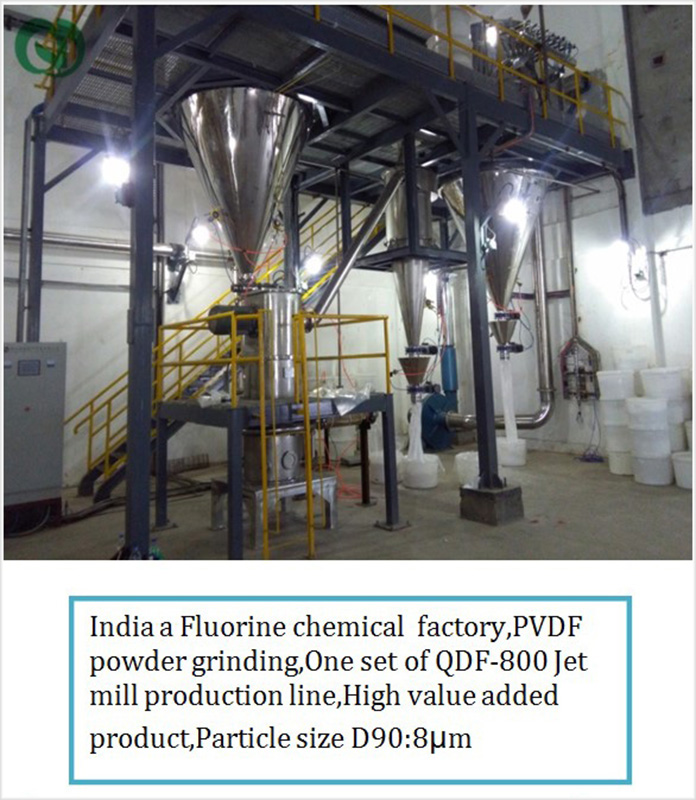
Material | Type | Diameter of the fed particles | Diameter of the discharged particles | Output(kg/h) | Air consumption (m3/min) |
Cerium oxide | QDF300 | 400(Mesh) | d97,4.69μm | 30 | 6 |
Flame retardant | QDF300 | 400(Mesh) | d97,8.04μm | 10 | 6 |
Chromium | QDF300 | 150(Mesh) | d97,4.50μm | 25 | 6 |
Phrophyllite | QDF300 | 150(Mesh) | d97,7.30μm | 80 | 6 |
Spinel | QDF300 | 300(Mesh) | d97,4.78μm | 25 | 6 |
Talcum | QDF400 | 325(Mesh) | d97,10μm | 180 | 10 |
Talcum | QDF600 | 325(Mesh) | d97,10μm | 500 | 20 |
Talcum | QDF800 | 325(Mesh) | d97,10μm | 1200 | 40 |
Talcum | QDF800 | 325(Mesh) | d97,4.8μm | 260 | 40 |
Calcium | QDF400 | 325(Mesh) | d50,2.50μm | 116 | 10 |
Calcium | QDF600 | 325(Mesh) | d50,2.50μm | 260 | 20 |
Magnesium | QDF400 | 325(Mesh) | d50,2.04μm | 160 | 10 |
Alumina | QDF400 | 150(Mesh) | d97,2.07μm | 30 | 10 |
Pearl power | QDF400 | 300(Mesh) | d97,6.10μm | 145 | 10 |
Quartz | QDF400 | 200(Mesh) | d50,3.19μm | 60 | 10 |
Barite | QDF400 | 325(Mesh) | d50,1.45μm | 180 | 10 |
Foaming agent | QDF400 | d50,11.52μm | d50,1.70μm | 61 | 10 |
Soil kaolin | QDF600 | 400(Mesh) | d50,2.02μm | 135 | 20 |
Lithium | QDF400 | 200(Mesh) | d50,1.30μm | 60 | 10 |
Kirara | QDF600 | 400(Mesh) | d50,3.34μm | 180 | 20 |
PBDE | QDF400 | 325(Mesh) | d97,3.50μm | 150 | 10 |
AGR | QDF400 | 500(Mesh) | d97,3.65μm | 250 | 10 |
Graphite | QDF600 | d50,3.87μm | d50,1.19μm | 700 | 20 |
Graphite | QDF600 | d50,3.87μm | d50,1.00μm | 390 | 20 |
Graphite | QDF600 | d50,3.87μm | d50,0.79μm | 290 | 20 |
Graphite | QDF600 | d50,3.87μm | d50,0.66μm | 90 | 20 |
Concave-convex | QDF800 | 300(Mesh) | d97,10μm | 1000 | 40 |
Black silicon | QDF800 | 60(Mesh) | 400(Mesh) | 1000 | 40 |