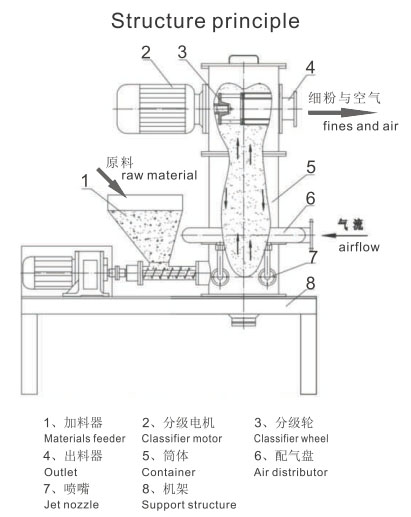
Product Description
Double Screw Cone Mixer machine equipment
1.the bearing outside, prevent the material from entering inside, then jam. 2.valve and valve core are casting parts, no deformation after long term use. 3.CNC process ensures good precision.Rotary valve
Horizontal spiral ribbon mixer
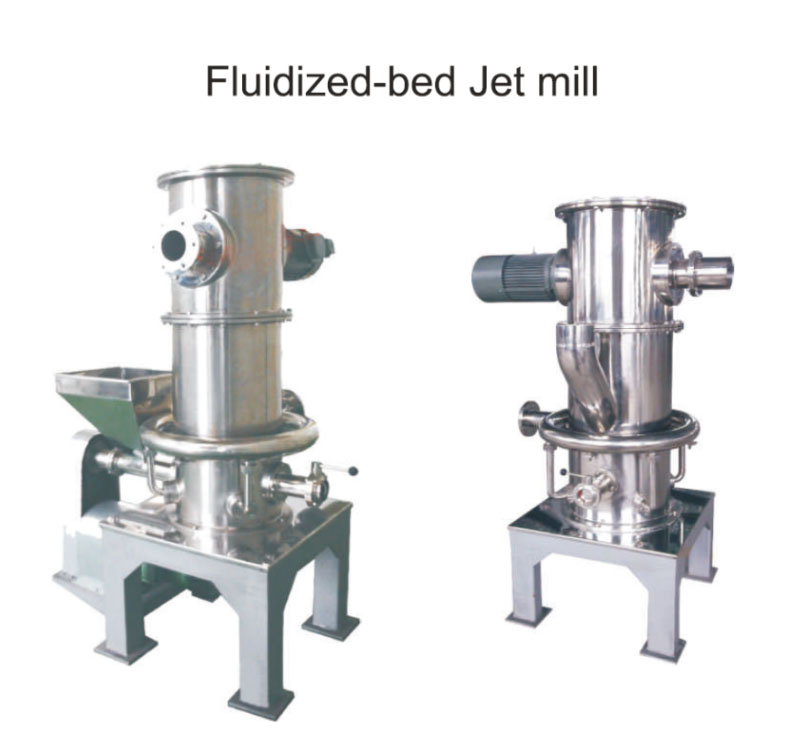
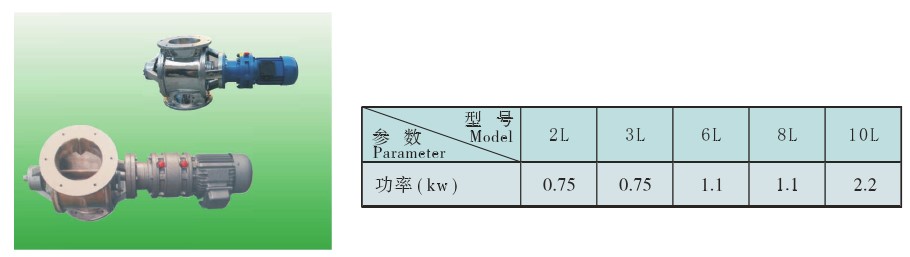
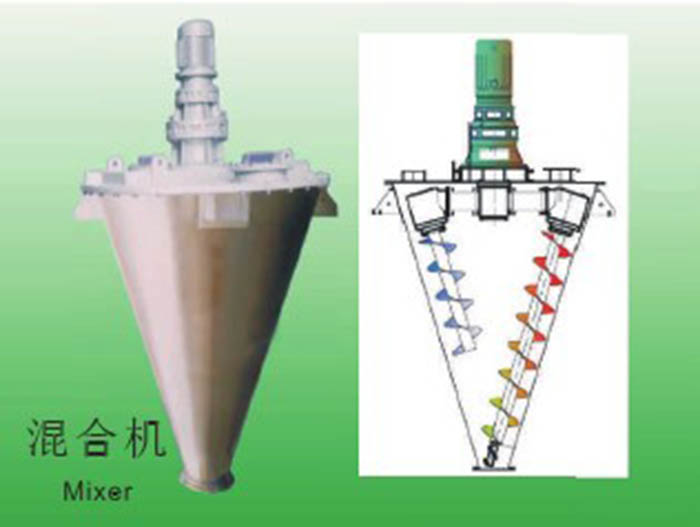
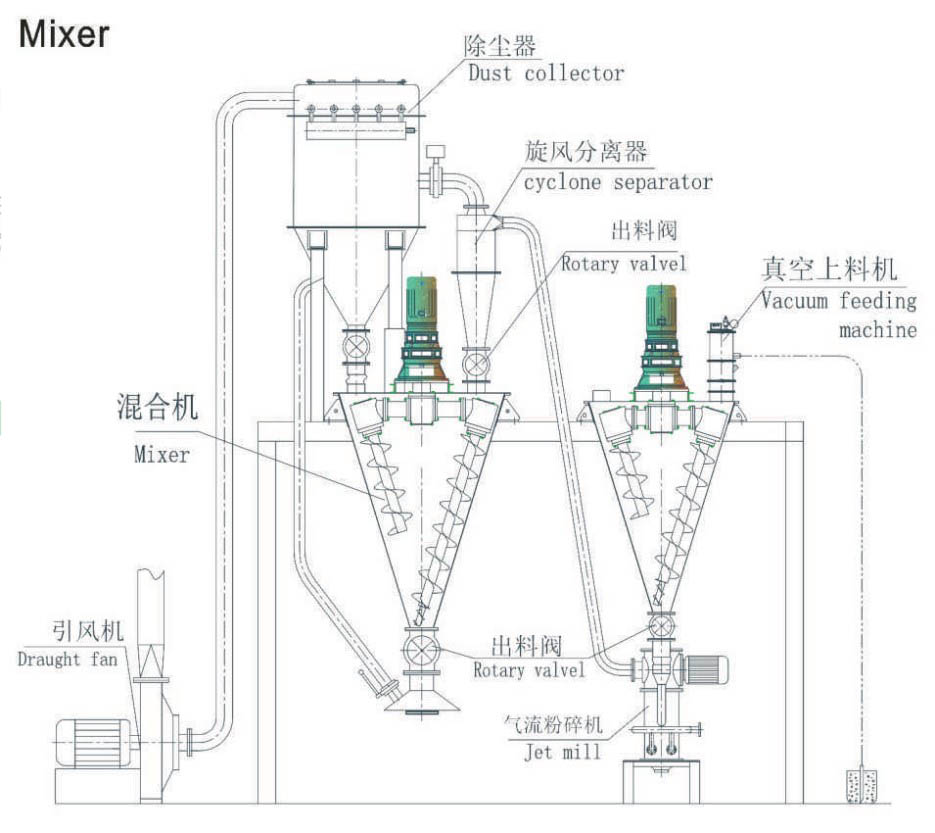

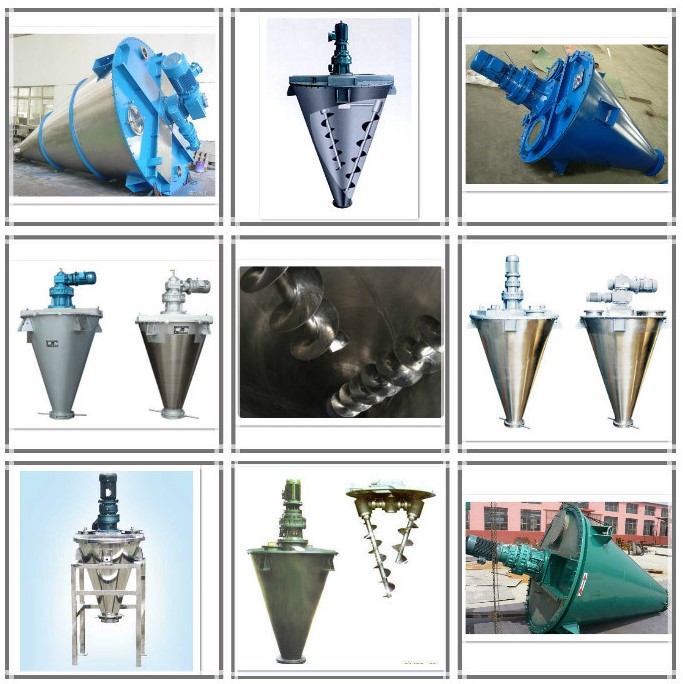
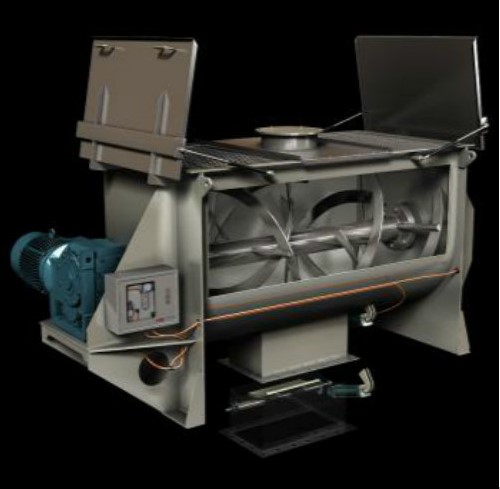
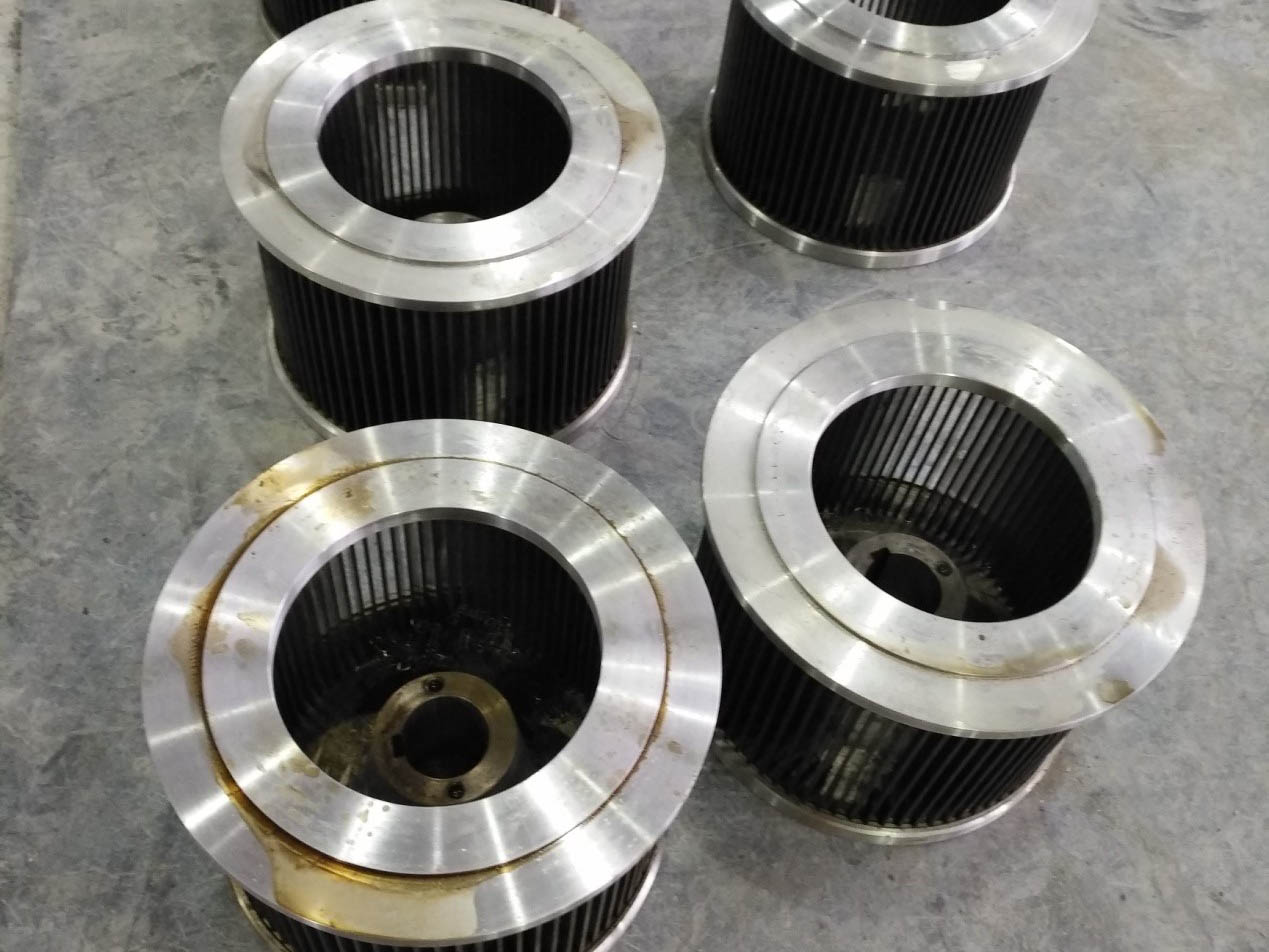
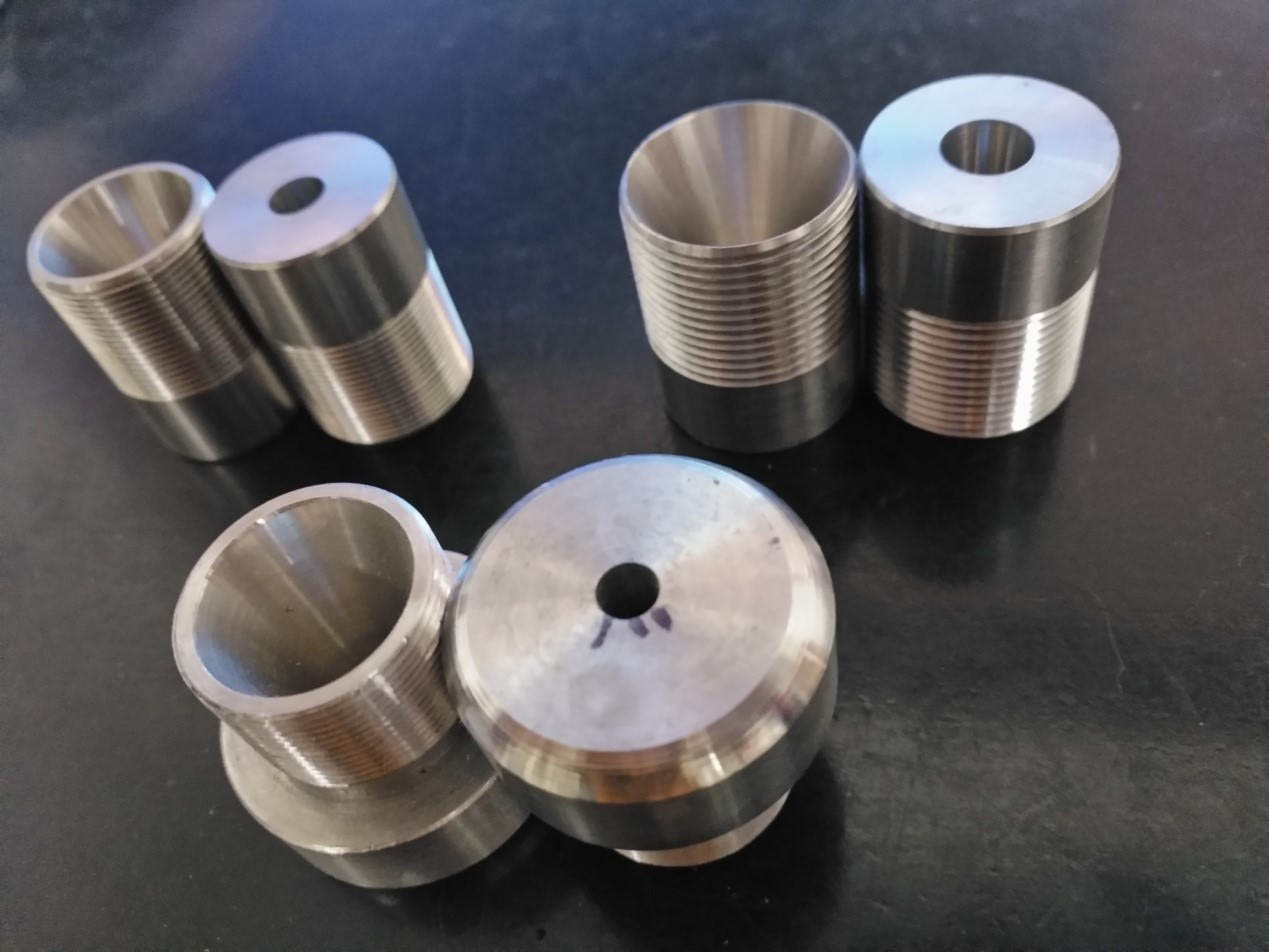