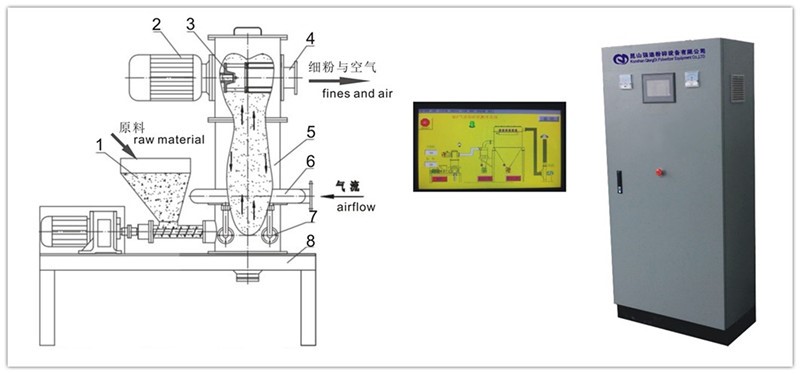
Product Description
WP/WDG System--Apply to Agrochemical Flow Scheme
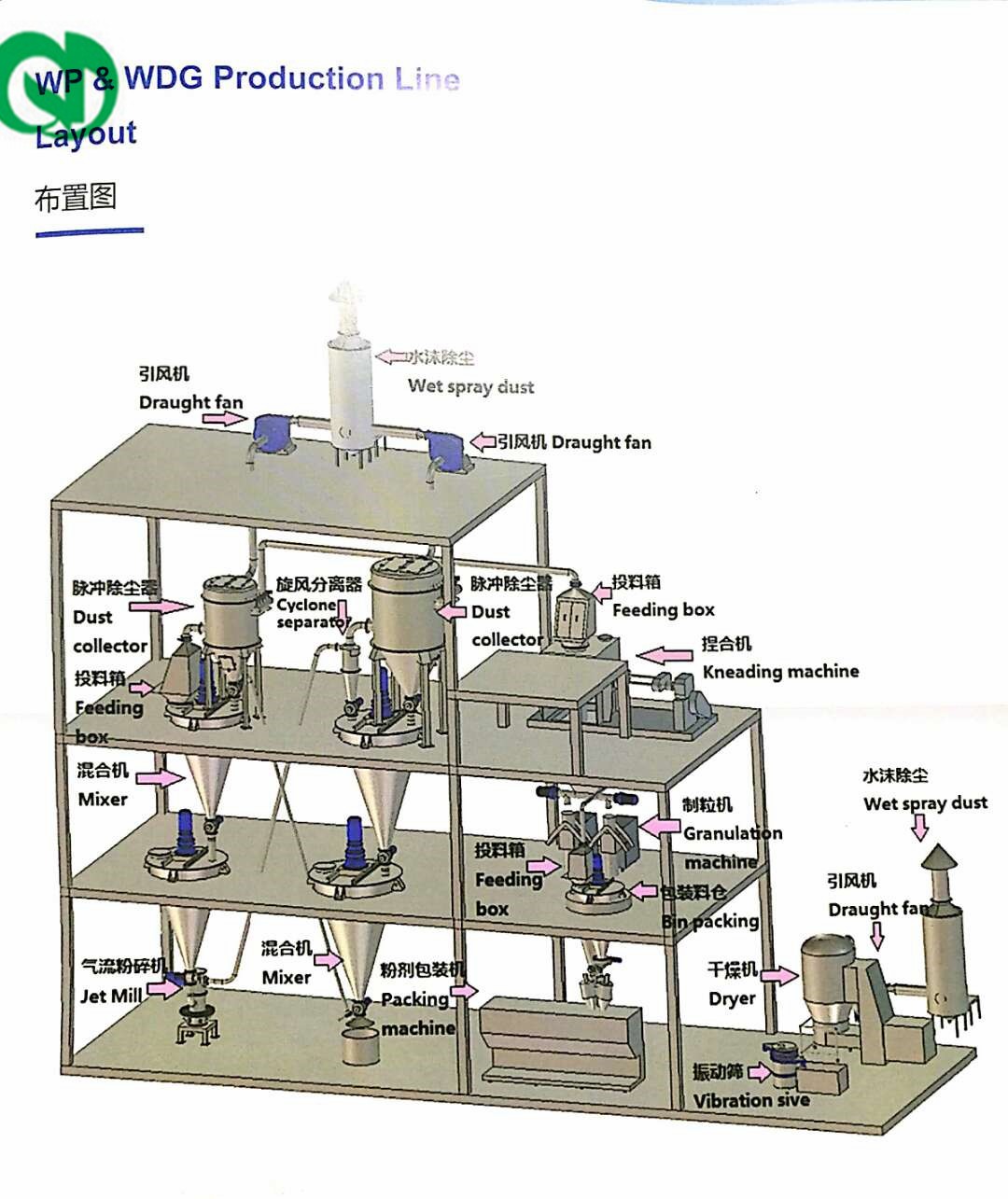
Flow Chart Of Fluidized-bed Jet Mill WP Line/WDG Line
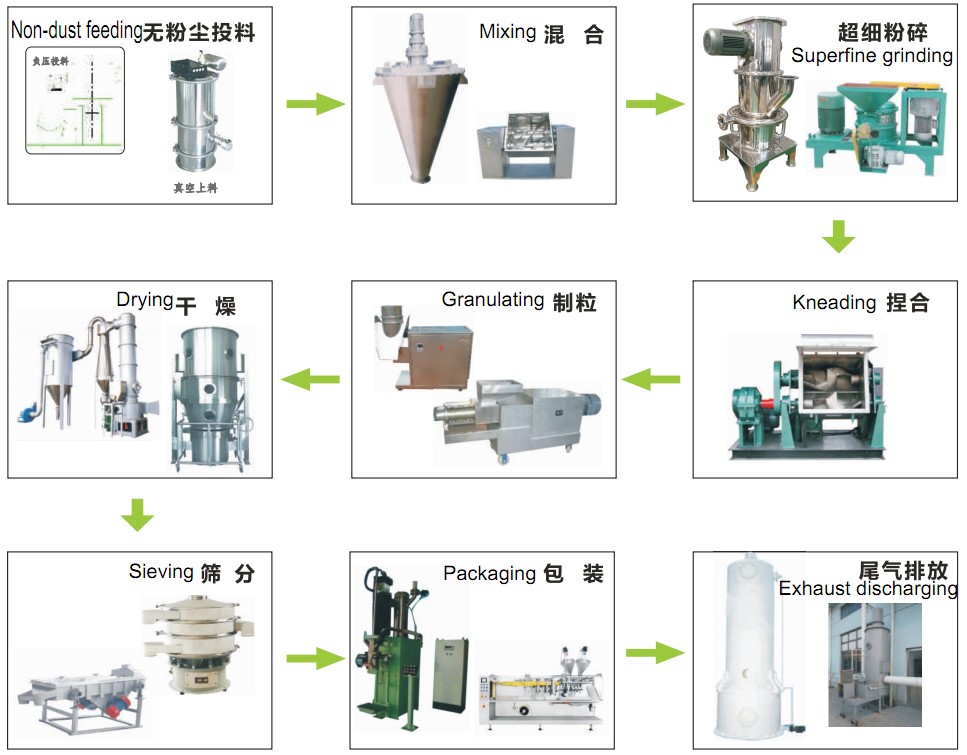
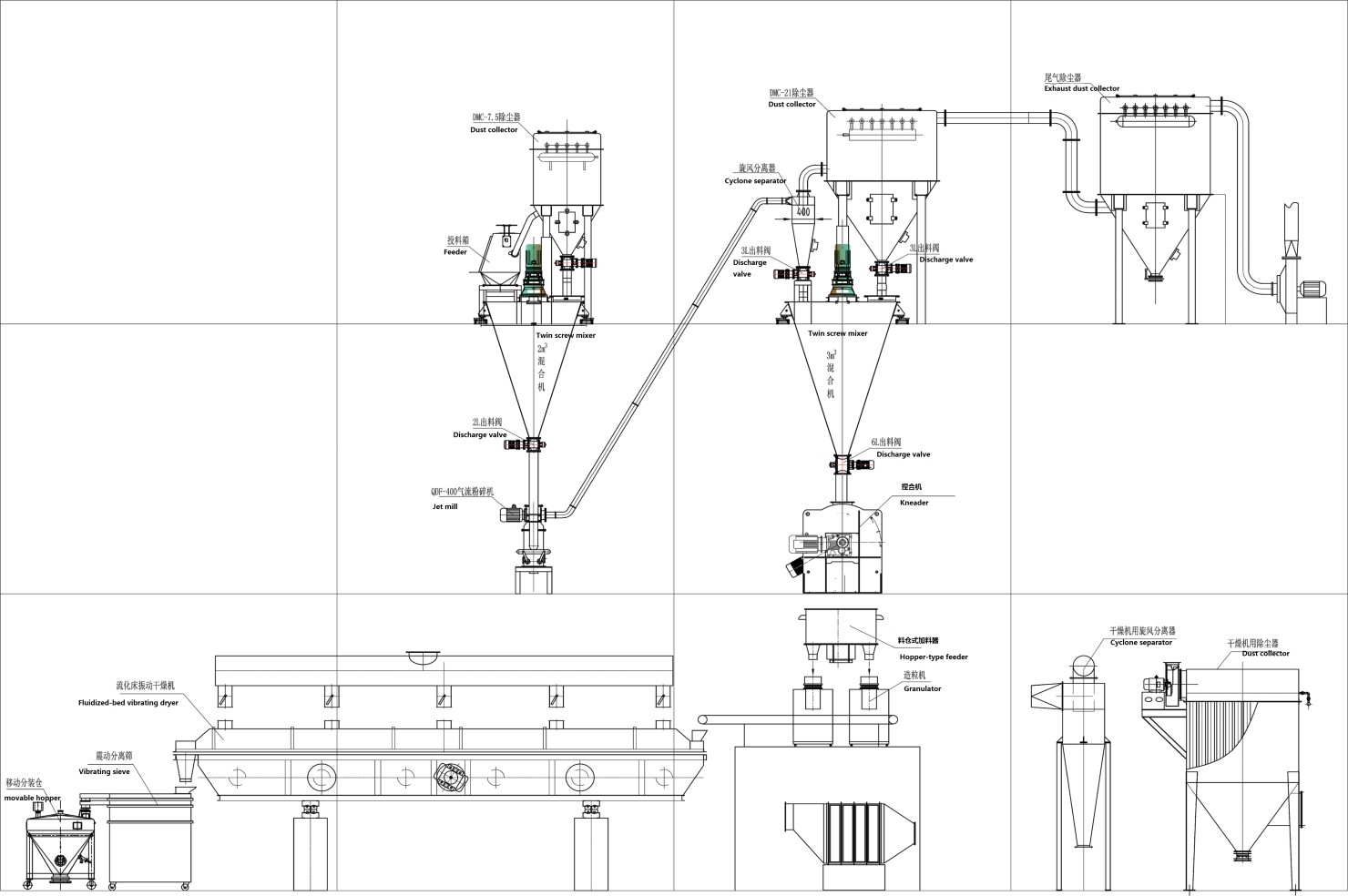
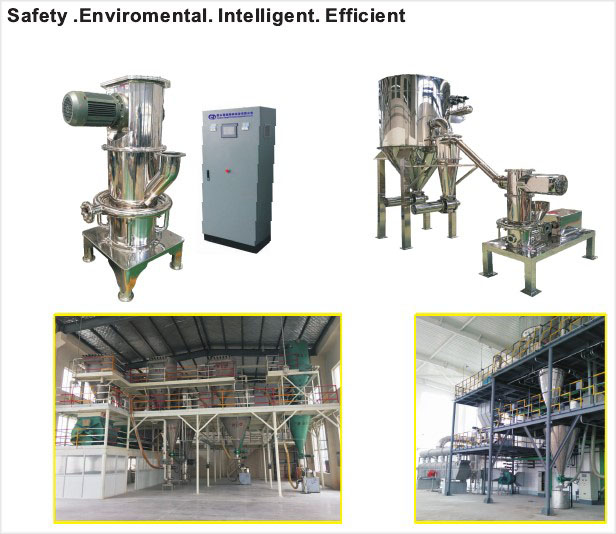
WDG process
First, the raw material will be transported into 1000L Buffer,then itto ZGH-1000 vertical mixer machine by Vacuum ZKS-6 for wet mixing then transport into XL-450 extrude granulator (3pcs) through 500L distributor for wet granule , then to QZL-1300 pelletor,and to ZQG-7.5 X 0.9 Vibrate Fluid-bed Dryer strip granules then ZS-1800 centrifugal vibration sieve for sieve to get required size granules.XL Rotary and Extrude Granulator
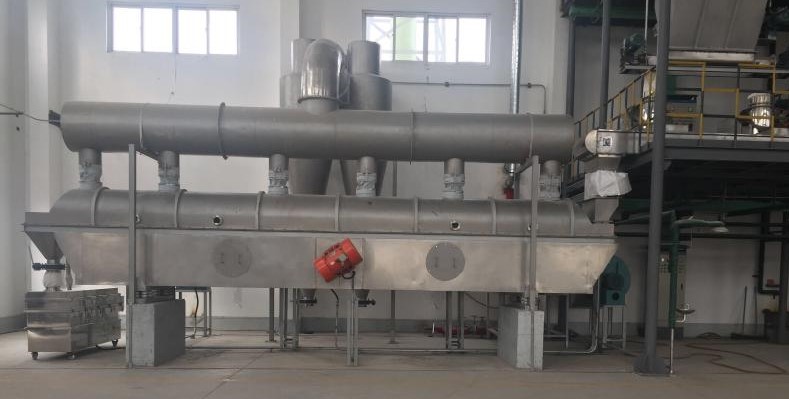
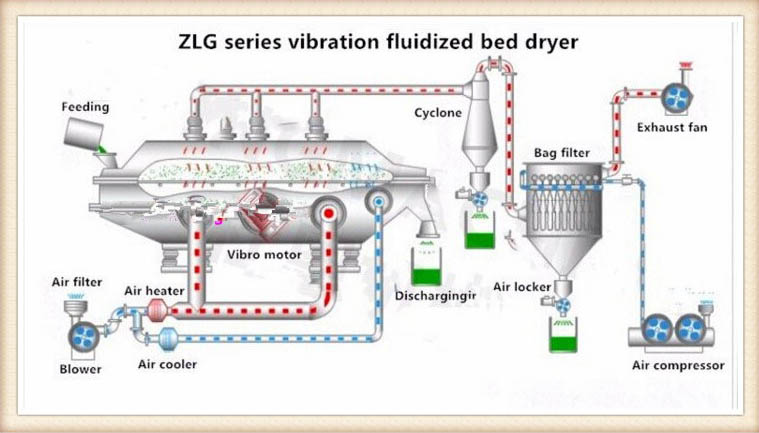
Vibrating fluid bed dryer for chemical powder
Vibrating fluid bed dryer for chemical powder
Working Principle
Vibration fluid bed is a new technology developed on the basis of static fluid bed. Mechanical vibration is added on the fluid bed. Wet material particles enter the air stream and form a fluid bed. The material is ejected due to exciting force. Vibrations of an air distributing plate incite the fluidization of material particles and the movement of material in the fluid bed. The fluid material contacts the hot air and at the same time carries on heat and mass transfer. The dried product is dischaged through the discharge port.
Characteristics
1. Uses the advanced vibrofluidization technology, the damage of dried material particle surface is small.
2. Steady movement, good adaptability.
3. Vibrations cause fluidization, the drying air flow rate is reduced, and a few particles are entrained.
4. The material residence time is consistent, product quality is uniform.
5. It is used for the drying of heat sensitive material in short time, such as, the surface water
drying of CUSO4·5H2O contained crystal water, MgSO4·7H2O.
Applicable scope
Can be used in dry or cooling process, applicable to the particle bulky or particles and not easy flow of irregular of products, or because to make particles less demanding and keep complete fluidization velocity of products and easy to bond, sensitive to temperature drying and contain materials gesso product surface water removal from.
Technical parameterModel | Fluidized bed area (M2) | Inlet air temperature (oC) | Outlet air temperature (oC) | Evaporation water capacity (kg) | Motor | |
Model | Kw | |||||
ZLG3×0.30 | 0.9 | 70-140 | 40-70 | 20-35 | ZDS31-6 | 0.8×2 |
ZLG4.5×0.30 | 1.35 | 70-140 | 40-70 | 35-50 | ZDS31-6 | 0.8×2 |
ZLG4.5×0.45 | 2.025 | 70-140 | 40-70 | 50-70 | ZDS32-6 | 1.1×2 |
ZLG4.5×0.60 | 2.7 | 70-140 | 40-70 | 70-90 | ZDS32-6 | 1.1×2 |
ZLG6×0.45 | 2.7 | 70-140 | 40-70 | 80-100 | ZDS41-6 | 1.5×2 |
ZLG6×0.60 | 3.6 | 70-140 | 40-70 | 100-130 | ZDS41-6 | 1.5×2 |
ZLG6×0.75 | 4.5 | 70-140 | 40-70 | 120-140 | ZDS42-6 | 2.2×2 |
ZLG6×0.9 | 5.4 | 70-140 | 40-70 | 140-170 | ZDS42-6 | 2.2×2 |
ZLG7.5×0.60 | 4.5 | 70-140 | 40-70 | 130-150 | ZDS42-6 | 2.2×2 |
ZLG7.5×0.75 | 5.625 | 70-140 | 40-70 | 150-180 | ZDS51-6 | 3.0×2 |
ZLG7.5×0.9 | 6.75 | 70-140 | 40-70 | 160-210 | ZDS51-6 | 3.0×2 |
ZLG7.5×1.2 | 9 | 70-140 | 40-70 | 200-260 | ZDS51-6 | 3.0×2 |
Fluid Bed Dryer For Granulation
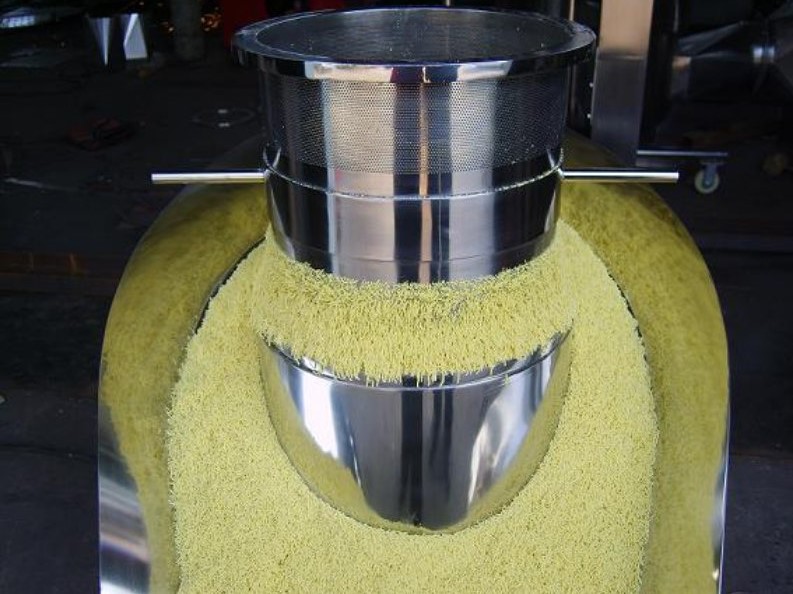
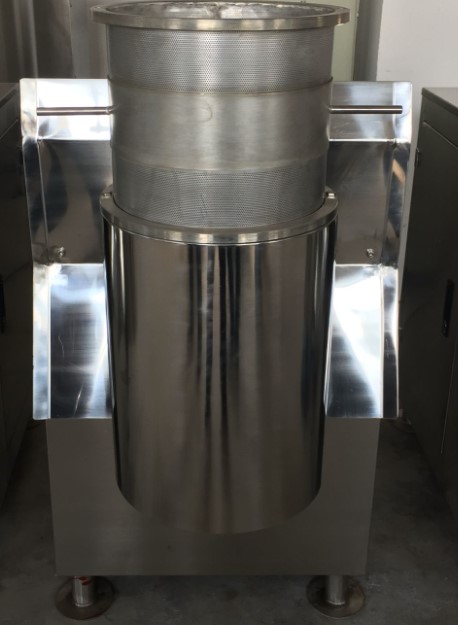
Ouput | 150-250kg/hour ( flake shape), 50-100kg/hour ( granule shape) |
Granule size | 0.5-2mm |
Max pressure | 294Kn(30T) |
Side sealing pressure | 9.8Kn |
Feeding motor | 2.2Kw |
Granulating Motor | 2.2Kw |
Compressing motor | 7.5Kw |
Feeding screw speed | 6-33 adjustable |
Compressing Wheel speed | 4-25 adjustable |
Dimension of compressing wheel | 240X100mm |
Weight ( approximately) | 2000Kg |
Main unit dimension | 1600X1000X2300mm |
Control cabinet dimension | 600X400X1300mm |
Size of milling knife(mm) | 300 | 400 |
Diameter of granule(mm) | Φ2~2.2(It may be in accordance with the requirements of customers) | Φ1.2~3(It may be in accordance with the requirements of customers) |
Overall dimesions(mm) | 700×540×1300 | 880×640×1300 |
Power of motor(kw) | 3 | 4 |
Weight(kg) | 350 | 400 |
Production capacity(kg/h) | 100~200 | 140~400 |
Full Stainless Steel High Speed Mixer
Principle LGH vertical type mixer is composed by bottom send material oars and high speed crushing oars,The bottom oars continuous send material to the top along the wall of the container. High speed crushing oars break up the material completely make the material cycle like vortex, to finish the uniformly mixing in a short time. Features of equipment LGH vertical type high speed mixing machine is the newest type high-efficiency mixer of our factory, which collected advanced technique of domestic and oversea.The main features are as following: 1.The bottom material oars continuously send the material to the top through the centrifugal force. And the top material drop to the bottom at the centre, to make the material cycle like vortex. 2.High-speed crushing oars break up the bulk material completely which send by the bottom oars. 3.The material can mix uniformly in a short time because of the two oars high-speed revolution. The mixing speed and uniformity is the best one in all kinds of mixing machine in domestic market. The uniformity is 100% mix. 4.Start the discharging valve, discharging speed is very fast, and the machine is easy to clean. 5.The machine contact parts were made by stainless steel, during the mixing process, the material will not volatilize, metamorphic and lost. 6.The machine suits for different proportional dry and wet material to mix, especially suits for mixing of chicken essence, dissolved medicine, dissolved drink and so on.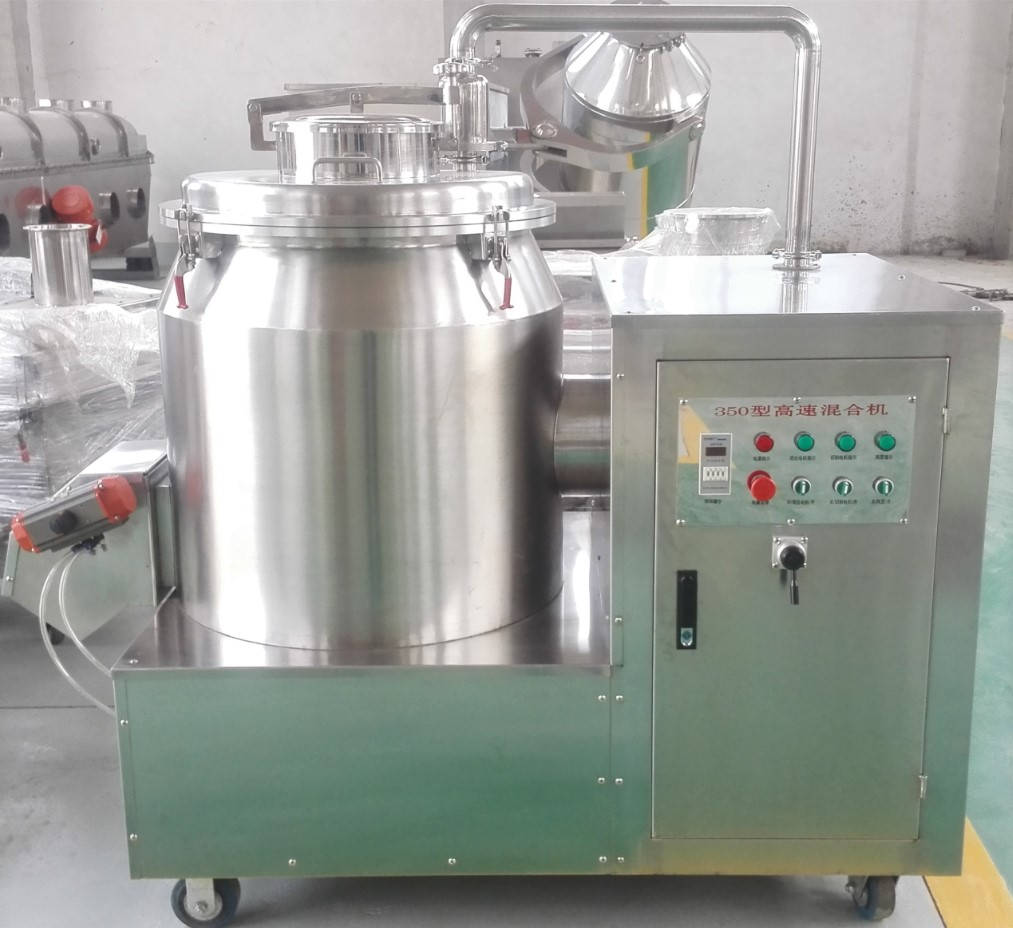
ZS Rorary vibro screen
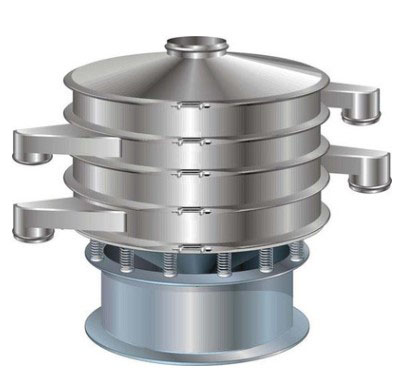
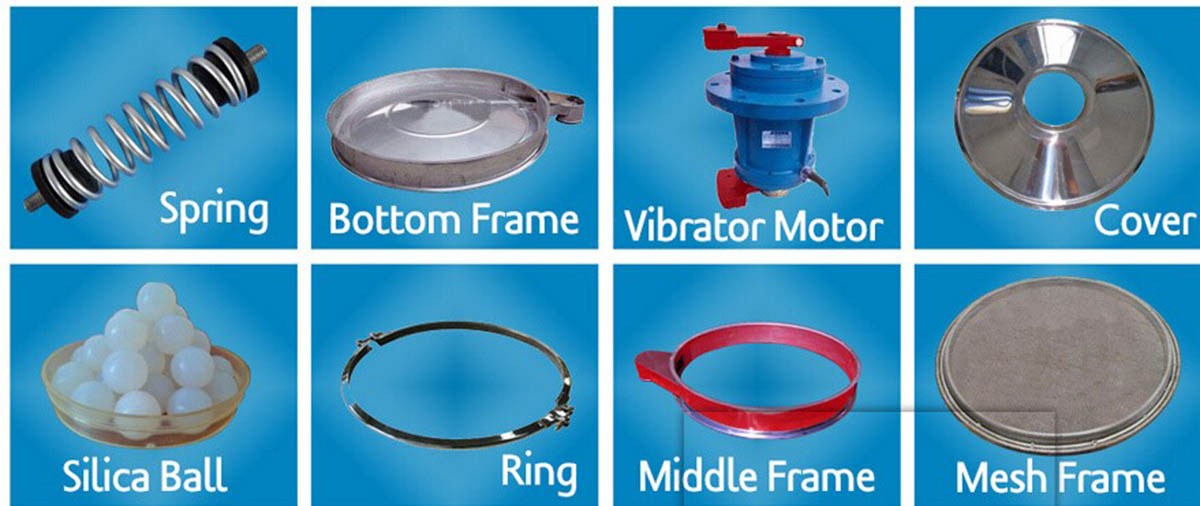
NG kneader
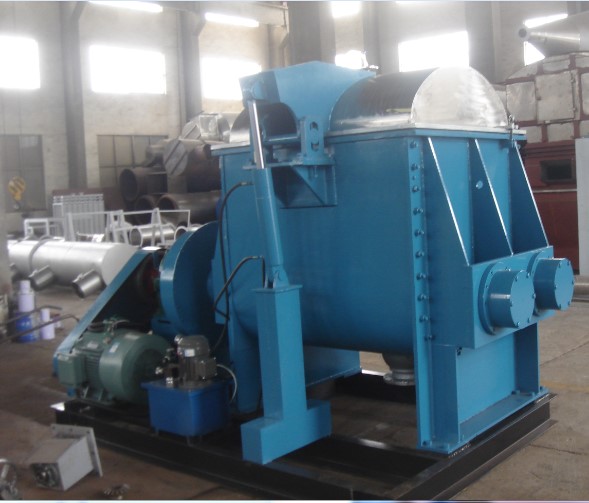
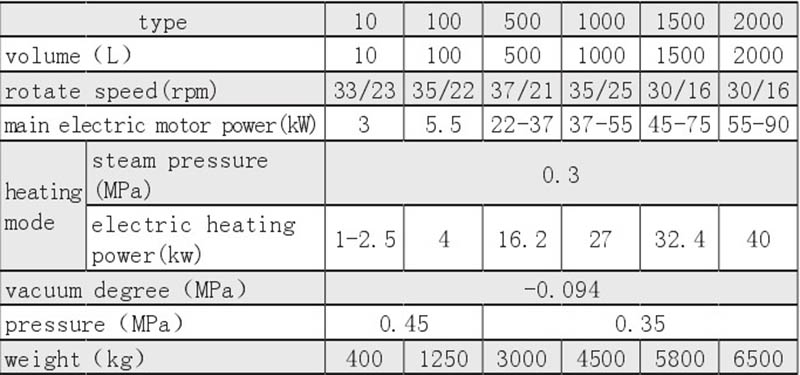
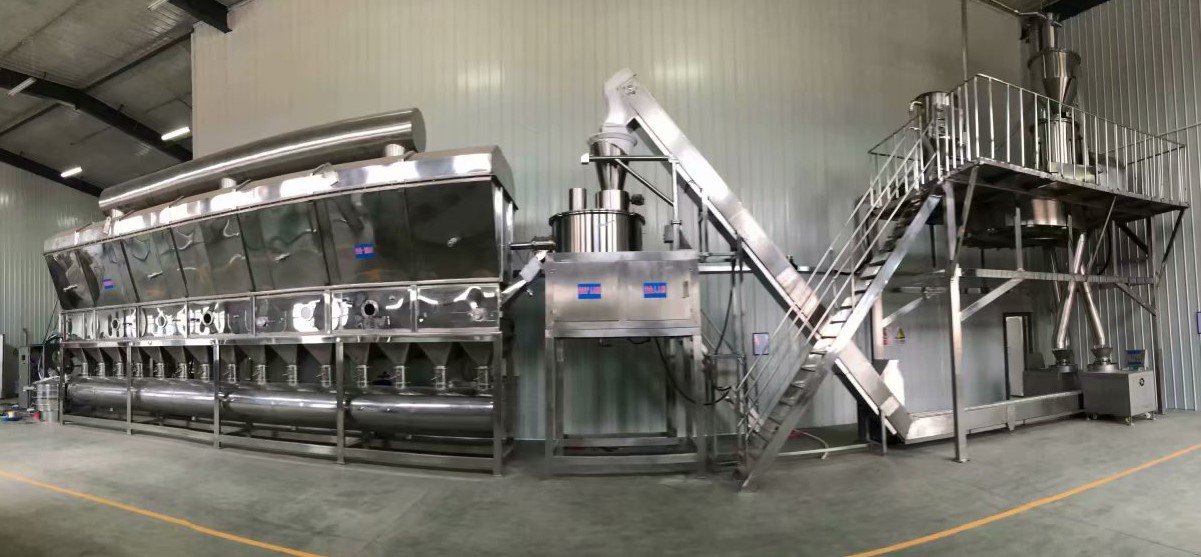
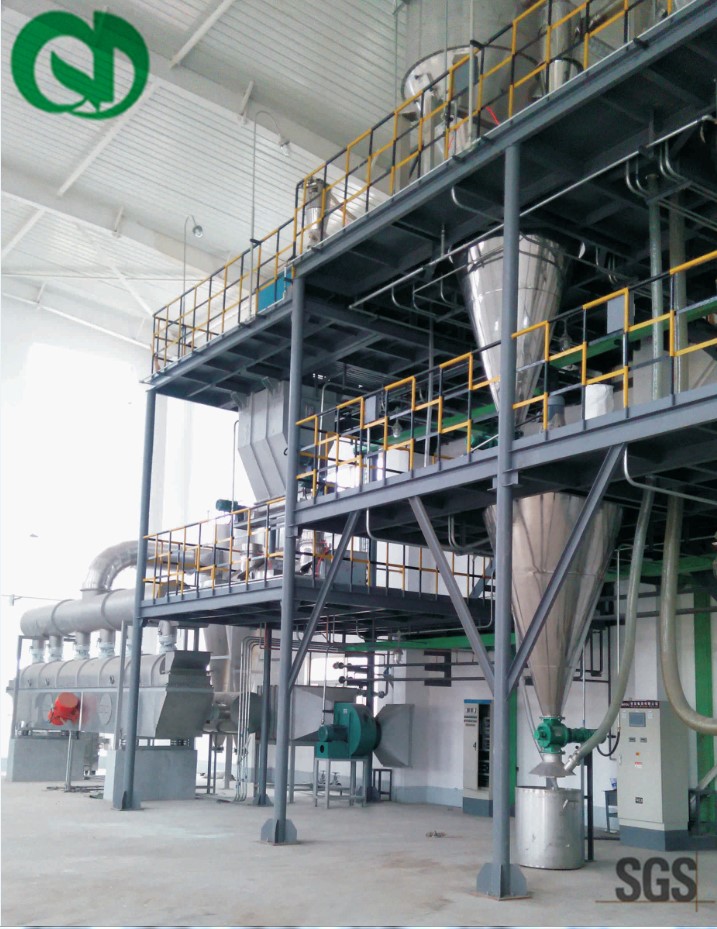
NG kneader
Project Definition - Feasibility and concept study - Cost and Profitability calculations - Timescale and resource planning - Turnkey solution, plant upgrade and modernization solutions Project Design - Knowledgable engineers - Using the latest technologies - Exploiting the knowledge gained from hundreds of applications across any industries - Leverage expertise from our experienced engineers and partnersPlant Engineering - Plant design - Process monitoring, control and automation - Software development and real time application programming - Engineering - Machinery manufacturing Project Management - Project planning - Construction site supervision and management - Installation and testing of instrumentation and control systems - Machinery and plant commissioning - Employee training - Support throughout production